Pinnacle Sensors, Inc.
The Pinnacle in Pressure Sensing Technologies
Quality You Know
ISO 9001 & AS9100 Conformance
Expectations We Meet
Strive for the top and you’ll reach it. That’s our motto, and our experience. We’ll work our hardest so that your most challenging goals, every time.
Application Solutions
Every sensing application has its own challenges and every challenge is unique in its own way. No project should suffer from compromise or paying too much for customization. Leonardo da Vinci once said “Engineering is a series of compromises”. At PSI, we don't believe your sensors need to be one.
Aerospace & Defense
Our aerospace pressure sensors are fully compliance to DO-160, MIL-STD-810, MIL-STD-461. Reliability you can trust for your ground-testing and airborne system.
Oil & Gas
With safety in mind, our team works with the industry experts hand-in-hand and together certified for industry explosion-proof and flame proof to be used in the hazardous locations. See our products certified to through our customer.
Military
MIL-SPEC
MIL-STD
Marine
Tailor to the Navy application, we design our sensor per MIL-V-2457B(SH) 9/16-18 threads and pass MIL-S-901D high shock testing.
Contact us for your unique system in the high shock environment.
Space
Compliance to MEDLI2-6005
Custom design
We incorporate CAD in all design phases and FEA for design stress / strain analysis. All custom sensors are made by quality manufacturing equipment, combined with precision instruments for testing and calibration.
A phone call away
Need expert advice on pressure measuring, or monitoring design and application? We welcome you to utilize our years of pressure sensing experience. A call to PSI may save you valuable time and money on design and installation. Most of your questions can be answered over the phone. Expert advice is just a phone call away.
Friendly support
Our support team is here to ensure things runs smoothly, so you can move forward with your projects.
PSI designs and manufactures custom sensors to interface with your equipment and system.
Glossary
Understand the industry terms
Reliability
Reliability is at the realm of our design and products to ensure your system get the monitoring it needs.
Pressure Sensors Spec.
We have a wide range of capability to suite your need. See what we can do to help your unique application.
Design you can trust
PE licensure is the engineering profession's highest standard of competence and assurance of quality. Our design blueprints and calculations are signed off by our P.E. so you can have a peace of mind.
Pressure Sensors Achieve Airworthiness
Airworthiness is the measure of an aircraft's suitability for safe flight.
Our pressure sensors are designed and tested conforms to DO-160 for airworthy condition for safe flight.

S-1000 SPECIFICATIONS
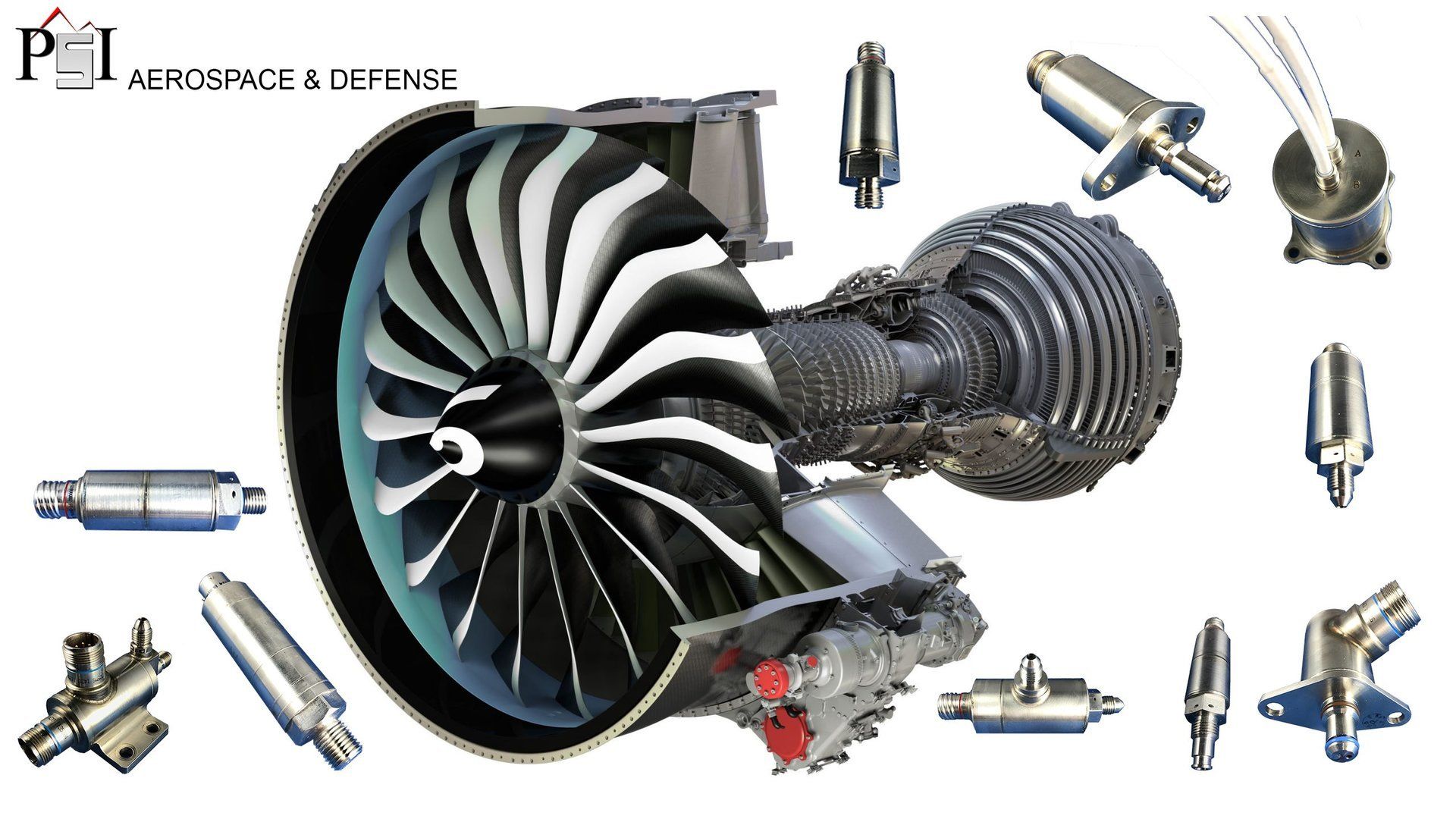
FEATURES
• NEW!
SOI oil-filled technology
• High operating temperature range up to 400°F (200°C)
• Extremely accurate over a wide temperature range
• Compliant to DO-160, MIL-STD-810, and MIL-STD-461.
• Technology can be easily tailored to meet specific application requirements, expending the limitation.
• Inquiry us with customize pressure fitting and electrical connector specific for your application.
APPLICATIONS
• Engine Oils/Fuels
• Hydraulic Fluids
• Flight Testing
• Jet Engine Testing
SENSOR
Total Error Band: < ±1.0 %FS (Include Static, and Thermal Error within Compensated Temperature Range)
Static Accuracy: < ±0.1 %FS (Include Linearity, Hysteresis, Repeatability)
Compensated Temp. Range: -55°F to 400°F (-48°C to 200°C)
Reference: Absolute, Gage, Sealed, Differential
Proof Pressure: 2X
Burst Pressure: 5X
Life Cycles (MTBF): > 10 million full scale cycles
ELECTRICAL
Supply Voltage: 0-10 Vdc
Output: 0-100 mV
Input/output Impedance: 5000 Ω
Insulation Resistance: > 10 GΩ @50VDC
MECHANICAL
Media Compatibility Types:
- JP-4, JP-5, JP-8 Grade Aviation Turbine Fuel Per MIL-T-5624
- Hydraulic Fluid Per MIL-H-5606, MIL-H-83282
- Engine and Transmission Lubrication Oil Per MIL-L-7808 and MIL-L-23699
- Aviation Gasoline Per MIL-G-5572 All Grades
Construction Material: 316 SST (Consult factory for other options)
ENVIRONMENTAL
Ambient Temperature: -55°F to 400°F (-48°C to 200°C)
Fluid Temperature (Medium): -55°F to 400°F (-48°C to 200°C)
Altitude: up to 50,000 Feet
Shock: 100 G-PK
Vibration: 10-5,000 Hz sine and random
Acceleration: 12 G levels per MIL-STD-810C
QUALIFICATIONS
Full Compliance to most demanding safety and qualification requirements
RTCA DO-160
Defines a series of standard environmental test conditions (categories) and applicable test procedures for airborne equipment. The purpose of these tests is to provide a laboratory means of determining the performance characteristics of airborne equipment in environmental conditions representative of those which may be encountered in airborne operation of the equipment.
MIL-STD-810
Emphasizes tailoring an equipment's environmental design and test limits to the conditions that it will experience throughout its service life, and establishing chamber test methods that replicate the effects of environments on the equipment rather than imitating the environments themselves. Although prepared specifically for military applications, the standard is often used for commercial products as well.
The standard's guidance and test methods are intended to:
- define environmental stress sequences, duration, and levels of equipment life cycles;
- be used to develop analysis and test criteria tailored to the equipment and its environmental life cycle;
- valuate equipment's performance when exposed to a life cycle of environmental stresses
- identify deficiencies, shortcomings, and defects in equipment design, materials, manufacturing processes, packaging techniques, and maintenance methods; and
- demonstrate compliance with contractual requirements.
MIL-STD-202
This standard establishes uniform methods for testing electronic and electrical component parts, including basic environmental tests to determine resistance to deleterious effects of natural elements and conditions surrounding military operations, and physical and electrical tests.
HALT-HASS
Highly Accelerated Lifetime Testing - Highly Accelerated Stress Screening to ensure the reliability of our products delivered on your hand.
MIL-STD-461
This standard establishes interface and associated verification requirements for the control of the electromagnetic interference (EMI) emission and susceptibility characteristics of electronic, electrical, and electromechanical equipment and subsystems designed or procured for use by activities and agencies of the Department of Defense (DoD).
PRESSURE SENSORS
ALL THE PRESSURE MONITORING AND MEASUREMENT YOU NEED, IN ONE PLACE, TAILORED TO YOUR DESIGN, AWAITING YOUR INSTRUCTIONS
DIFFERENTIAL PRESSURE TRANSDUCER
PSI Differential Pressure Sensors are perfect solution for your demanding harsh environment. It is designed through FEA stress analysis for proof / burst pressure, and testing for harsh and hazardous location process monitoring for intrinsically safe and explosion proof areas including cULus, ATEX and IECEx.
Working closely with oil and gas, makes our transducers one of the most reliable pressure monitoring solution in the industry.
ABSOLUTE, GAGE, SEALED-GAGE
OPTIONS
Connection Solutions
At PSI, we specialize in design and customize pressure fitting connections and electrical connectors to fit your need. These are some of standard options we are offering. Contact us for special options.
Fitting Options
- 1/4-18 MNPT (External Thds)
- 1/4-18 FNPT (Internal Thds)
- 1/8-27 MNPT (External Thds)
- 1/8-27 FNPT (Internal Thds)
- 7/16-24 UNF Male SAE #4 (J1926)
- 9/16-18 UNF Male SAE #6 (J1926)
- 9/16-18 UNF Female SAE #4 (J1926)
Electrical Options
- Wires
- Ribbon Cable, 28 AWG
- Molex
- Mini DIN Connector 43650-C
Standard Pressure Range inPSIA, PSIG, PSID
- 0-5 PSI
- 0-10 PSI
- 0-50 PSI
- 0-100 PSI
- 0-200 PSI
- 0-500 PSI
PSI - POUND PER SQUARE INCH WITH THE FOLLOWING SPECIFIC
PSIA - ABSOLUTE
PSID - DIFFERENTIALPSIG - GAGE
* See our glossary for details on differential pressure
Output Options
- 0-100 mV
- 0.5-4.5 Vdc
- 0-5 Vdc
- 1-5 Vdc
- 0-10 Vdc
- 4-20 mA
Bidirectional Output Optionsfor Differential Pressure Transducers
Example shown with ±50 psid
0-5 Vdc BD transducer
0 Vdc -50 psid
2.5 Vdc 0 psid
5.0 Vdc +50 psid
4-20 mA BD transducer
4 mA -50 psid
12 mA 0 psid
20 mA +50 psid
PROUDLYDESIGNEDFOR YOU
Every product we design aims to tailored for your specific applications
Our skilled professionals are here to help you choose & design the correct components for your pressure system every step of the way. We specializes in providing custom-design electro-mechanical sensors for OEM applications for numerous industrial and medical applications, including aerospace, automotive, medical scales, R&D, and racing sports, in both low and high volume projects at lowest cost possible. PSI supplies complete custom sensing solutions to all industries, with quick turn around from design drawing board to sensors in customers' hands. PSI employs the latest technologies for every custom project.
TECH SUPPORTS
OUR CAPABILITIES
PRESSURE RANGE
1 PSI Full Scale to 10,000 PSI Full Scale
Absolute, Gage, Sealed Gage, and Differential
Hermetically Sealed True Gage
TEMPERATURE RANGE
-200 to +550 °C (-328 to +1022 °F) Ambient and Medium Temperature
MEDIA TYPES
All Types of Engine Oils, Fuels, Hydraulic Fluids, and Air
BRIDGE RESISTANCE
350 Ohms
1000 Ohms
1500 Ohms
3000 Ohms
5000 Ohms
PROOF PRESSURE
3X to 100X Pressure Overload, Unidirectional or Bidirectional
REDUNDANCY
Dual or Triple Independent Sensor Output Redundancy
SHOCK & VIBRATION
100 G pk, Sine & Random 10 to 5,000 Hz
WIRE CONNECTIONS
Vdc VOLTAGE OUTPUT CONNECTION
RED: + EXCITATION / + INPUT
Connect to your power supply + terminal
BLACK: - EXCITATION / - INPUT
Connect to your power supply - terminal
GREEN: + SIGNAL / + OUTPUT
Connect to your DMM + terminal (HI)
*Connect power supply - terminal to DMM - terminal (LO)
4-20 mA CURRENT LOOP
RED = + EXCITATION (+INPUT)
CONNECT TO POWER SUPPLY + TERMINAL
BLACK = + CURRENT OUTPUT
*CONNECT TO CURRENT I OUTPUT ON YOUR DMM
CONNECT POWER SUPPLY - TERMINAL TO DMM - OUTPUT TERMINAL
0-100 mV OUTPUT CONNECTION
RED: + EXCITATION / + INPUT
Connect to power supply + terminal
BLACK: - EXCITATION / - INPUT
Connect to power supply - terminal
GREEN: + SIGNAL / + OUTPUT
Connect to DMM + terminal (HI)
YELLOW: - SIGNAL/ - OUTPUT
Connect to - terminal to DMM - terminal (LO)
4-20 mA to 1-5 Vdc Conversion Connection
RED = + EXCITATION (+INPUT)
CONNECT TO POWER SUPPLY + TERMINAL
BLACK = + CURRENT OUTPUT
CONNECT TO DMM + TERMINAL (HI)
*CONNECT POWER SUPPLY - TERMINAL TO DMM - OUTPUT TERMINAL (LO)
ADD A 250 OHM RESISTOR BETWEEN HI & LO ON YOUR DMM TERMINALS AS ILLUSTRATED
EXPLOSION PROOF / FLAMEPROOF
EXPLOSION PROOF / FLAMEPROOF
Our sensors have obtained number of UL and CSA approvals and are currently servicing in The Oil & Gas Industries.
N. America
UL 1203, 60079-0, 60079-1, 61010-1
CSA C22.2 60079-0, 60079-1, 61010-1
Class I, Groups A, B, C and D;
Class II, Groups E, F, G;
Class III
Class I, Zone 1, AEx d IIC T3/T5
Class I, Zone 1, Ex d IIC
Weld Penetration Studies
How do we know our sensors are proven to meet or exceed the stringent explosion proof tests by numerous agencies such as UL, and delivers peace of mind regarding explosion hazards for users, inspectors and regulators? We dissect our sensors' welds, and study the weld penetration. Our sensors are incorporated in instruments/equipment in the UL certified in the oil & gas industries currently serving the harshest hazardous locations in the oil & gas field.